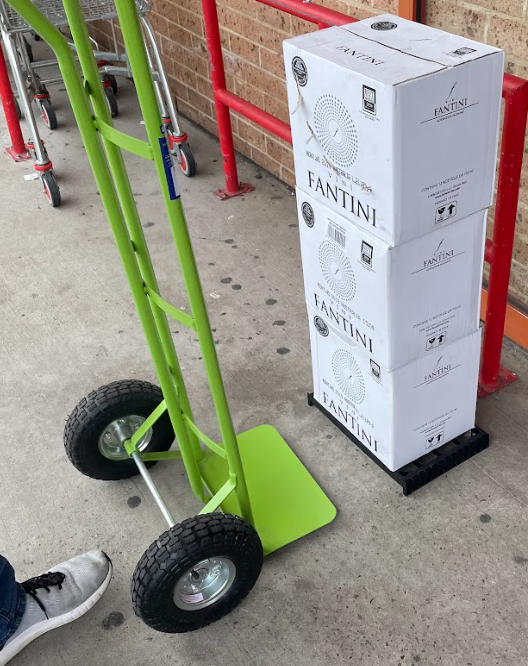
Reduce workplace injuries
| James Christie
Introduction
Workplace injuries are a significant concern for all types businesses in Australia, with recent data showing that over 497,300 individuals experienced a work-related injury or illnesses in 2023, with a notable percentage of these incidents related to 'lifting, pushing, pulling or bending' activity - a value provided from the Australian Bureau of Statistics. This value just emphasises just how implementing the right beverage handling system can significantly reduce workplace injuries and create a safer working environment for bottle shops, RSL’s, pubs and clubs..
The Relevance of an Efficient Beverage Handling System
The beverage industry is made up of activities that involve moving, lifting, and handling of various products with varying weights. The implementation of efficient beverage handling systems is pivotal in ensuring the safety and well-being of employees. Below are ways in which a good system can help reduce workplace injuries:
Improved Ergonomics
By adopting ergonomically designed equipment and processes, the strain on workers is significantly reduced. This minimises the risks associated with manual handling tasks and consequently reduces the likelihood of injuries. Think of doing the laboursome task multiple times per minute, then multiple by the hour and so on.
Automated Handling Procedures
Automation in handling procedures minimises the necessity for manual lifting, therefore reducing the risk of injuries associated with these tasks. By having the product already placed upon Mini Pallets, the person needing to move the products will not need to lift the item without a fulcrum or trolley. Reducing the need to lift another item is lowering the risk of injury to that team member.
Streamlined Work Processes
Streamlining work processes, particularly with the concept of goods receiving and use of vertical storage This substantially enhances workplace efficiencies. By implementing Mini Pallets into the receiving process, manual handling is reduced for anytime the goods need to be moved or transported. Additionally, vertical storage solutions optimise space and ensure that items are stored safely and securely, mitigating the risk of falls or other related incidents. It also uses cool rooms spaces more productively allowing people to fit more in their costly investment.
Buy Mini Pallets for Enhanced Safety
Mini Pallets are revolutionising the handling of beverages in the alcoholic and soft drink industries. The Mini Pallets light weight nature allows people to be able to store them easy, promotes inclusion for all employees to be able to maneuver heavy items, and the best news - they are made here in Australia. They facilitate easier and safer movement of beverage products within the workplace, significantly helping to reduce workplace injuries.
Economic Implications
The economic toll of workplace injuries is substantial. In Australia, work-related injuries and illnesses cost the economy approximately $28.6 billion annually, suggesting a pressing need for improved workplace safety measures. Our product is on the cusp of changing industry. As it was for the milk crate, the Mini Pallet will assist many different people in various businesses work safer and smarter.
Conclusion
The best performing beverage handling system is not just an investment in equipment but an investment in the safety and well-being of employees. As the data suggests, the initiative to reduce workplace injuries is not only a moral obligation as a business owner or manager, but also a national economic burden if we turn a blind eye. Through the careful selection and implementation of a unique beverage handling system, companies can significantly mitigate risks, ensure compliance with safety regulations, and foster a conducive work environment for all. This is all before we start to talk about reducing damage to stock!